什么是基于接触式探头的磨床“机上测量”?
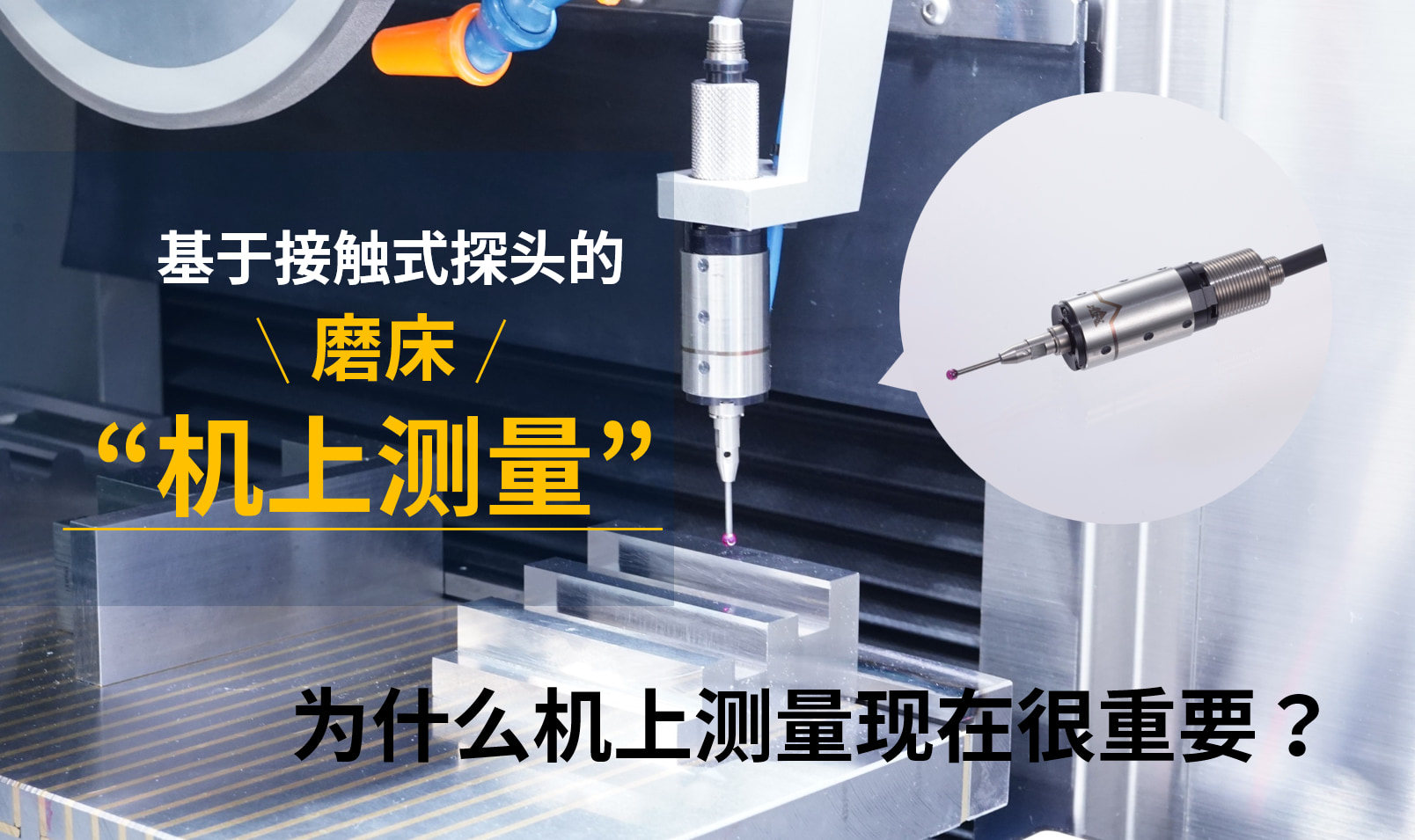
“CNC平面磨床”掌握着工件精加工品质。
磨削加工对精度的要求十分苛刻,你是否有以下感受?
- “三坐标测量机等的机外测量花费在设置及移动上的时间很多……”
- “因人而异的测量方法存在误差……”
- “想减少测量后的返工及追加加工……”
本文将以解决此类课题的“机上测量”为主题进行讲解。
若您打算改善包括磨削加工在内的制造工序,请不要错过此篇内容。
本文内容汇总
- 了解轻松进行加工准备及尺寸测量的方法
- 详解磨床“机上测量”的优点
- 了解引进CNC平面磨床机上测量的方法
目录
何谓机上测量?与机外测量的区别
“不太了解机上测量”的人应该不在少数吧?
下面先简单复习一下。
机上测量
機上測机上测量是指“在机床上测量加工件(工件)”。
本文中的机床是指平面磨床,其他诸如加工中心及CNC车床等各种机床也在实施机上测量。
测量仪器主要使用“接触式探头”这种接触式传感器。这是利用传感器接触工件时的机械位置信息测量工件尺寸的方法。(图像1)
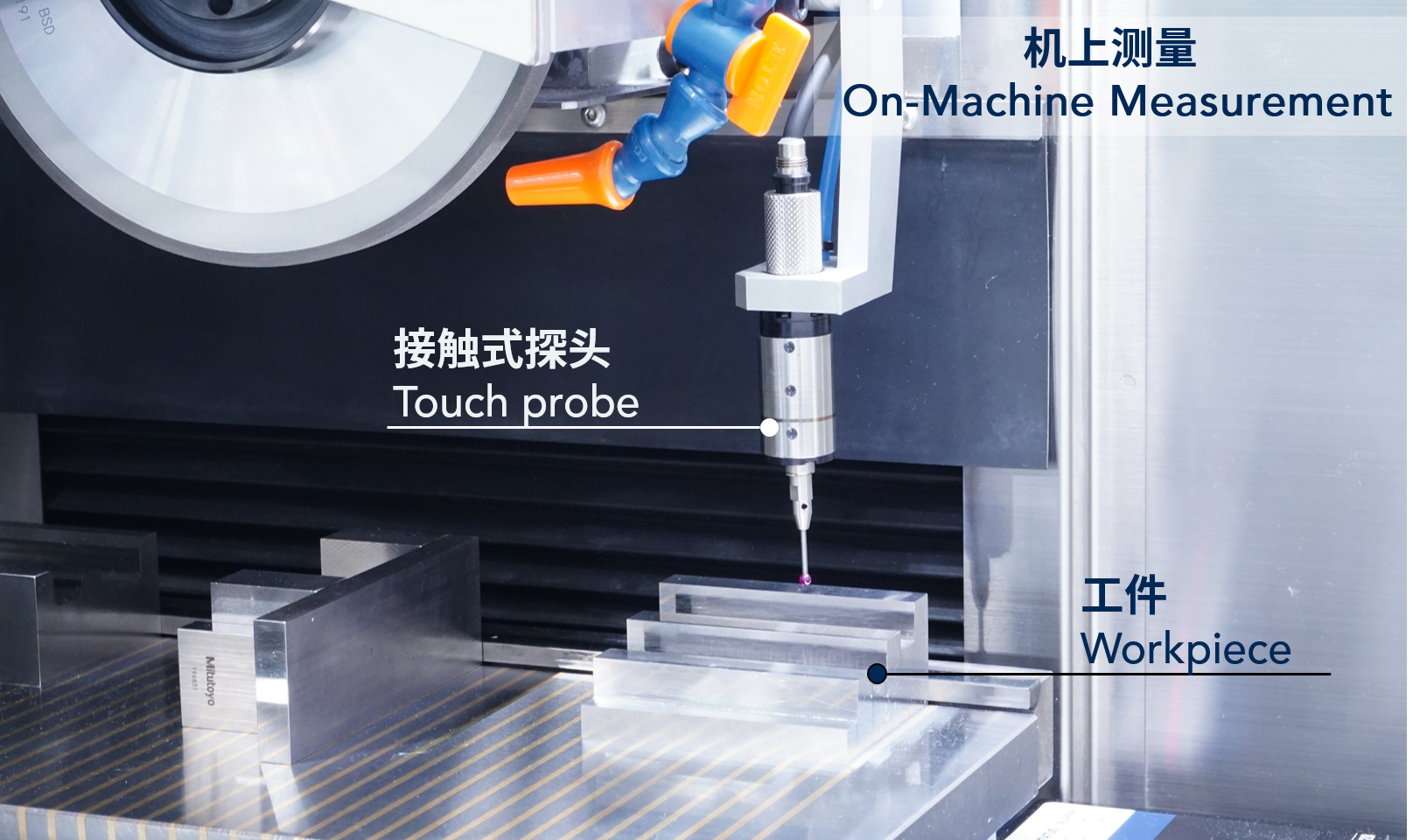
机外测量
机外测量是指“在机床外部测量加工件(工件)”。
将加工完成的工件从机床中取出,使用三坐标测量机、卡尺、孔径规及游标卡尺等测量仪器进行测量的方法。
虽然根据要求精度而异,但通常在实施温度管理的测量室进行测量,这样可以确保测量的精度。
若测量未达到公差,通常会将工件返回机床进行追加加工。
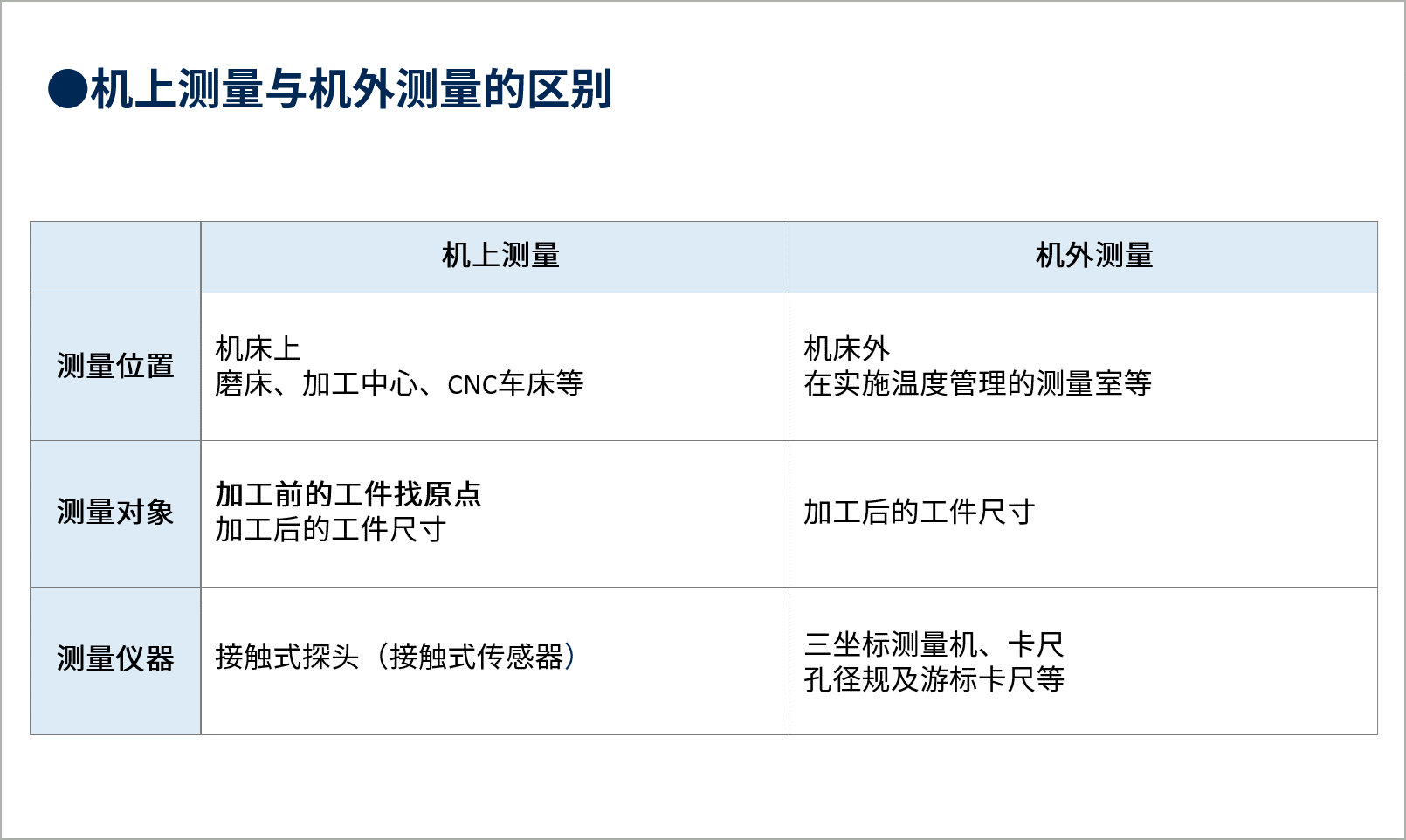
在讲解机上测量前,我们先来复习以下磨削加工周期
采用机上测量还是机外测量,将会对磨床加工周期的工时产生较大影响。
在此简单复习一下作为前提的“磨削加工周期”。
CNC平面磨床通常主要按照以下1~6个步骤(参看插图)进行磨削加工。(本文中省略砂轮整修和精修)
- 步骤1:通过“砂轮抵磨作业※1”确认加工起始点
- 步骤2:确认被磨削材料(工件)的加工起始点(测量厚度)
- 步骤3:加工周期
- 步骤4:测量工件厚度
- 步骤5:(若厚度未达标)追加加工
- 步骤6:测量、完成
此处步骤4与6的测量选择机外还是机上测量,将会大大改变整个工序的工时。
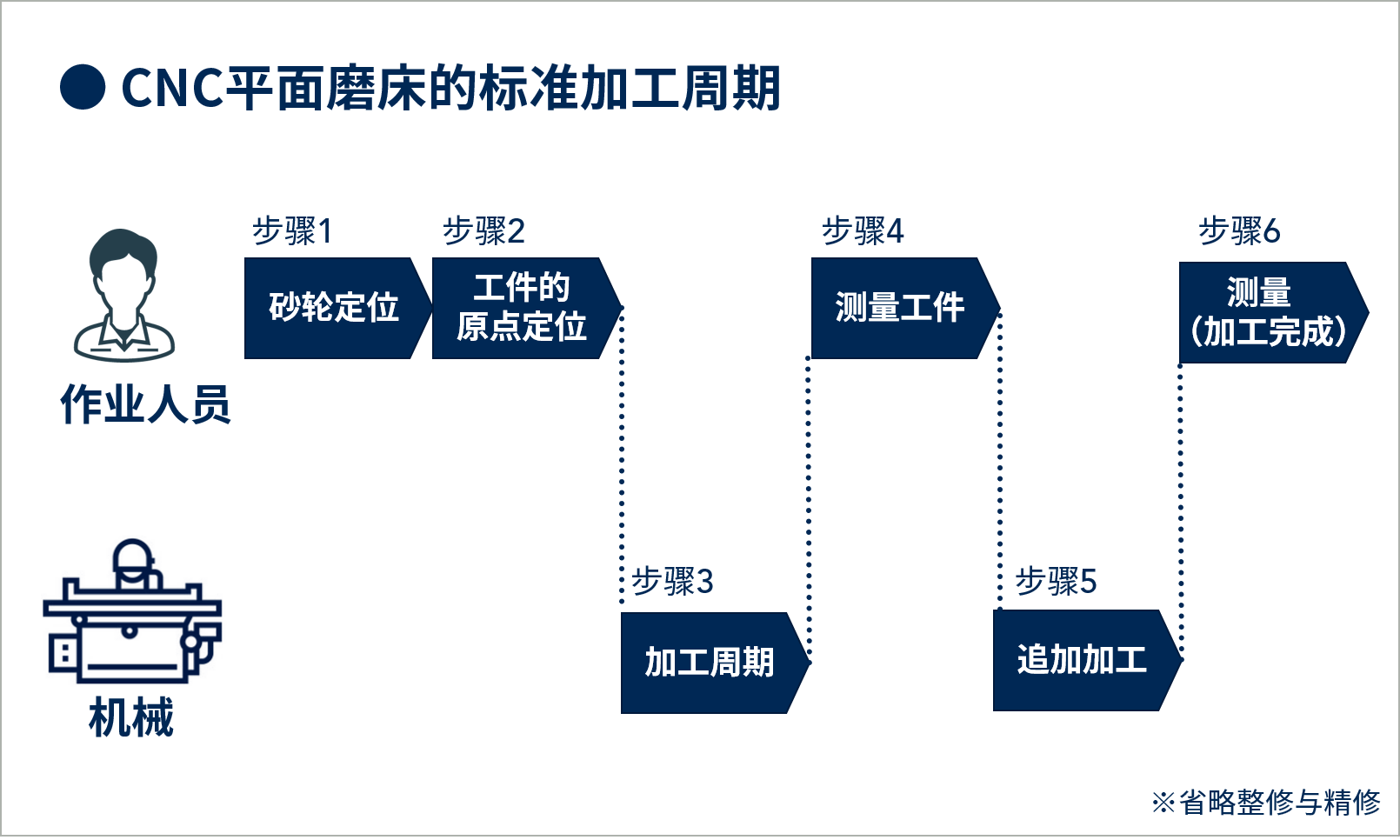
下一个
①实施机外测量时
②实施机上测量时
下面我们分别模拟以①与②的测量方法实施测量时的工时,进行比较验证。
通过工时了解到的“机外测量”的暗藏缺点有哪些?
通常加工后测量工件,若偏离容许公差,便要将工件返回加工工序进行追加加工以满足标准。
机外测量在这个过程中存在以下应削减的“不必要的工序”。
- 取出工件的作业
- 人员移动
- 再次安装工件的准备作业
- 根据测量结果(偏离公差)进行的返工
- 等待测量的工件的滞留
这些问题会导致出货前的前置时间过长,并增加提高成本的工时,成为了现场要解决的课题。
验证1:模拟机外测量
我们通过简单示例来模拟“机外测量”所需的工时。
(例)①加工 ⇒ ② 测量 ⇒ ③ 追加加工⇒ ④测量的周期
在此周期内会发生:
・人员移动:3次
・准备作业:3次(=加工准备:1次、安装至测量仪:2次)※仅初次准备必须实施(参看图1)
各装置的工件安装、拆卸及定位等繁琐的准备作业每次都会发生。
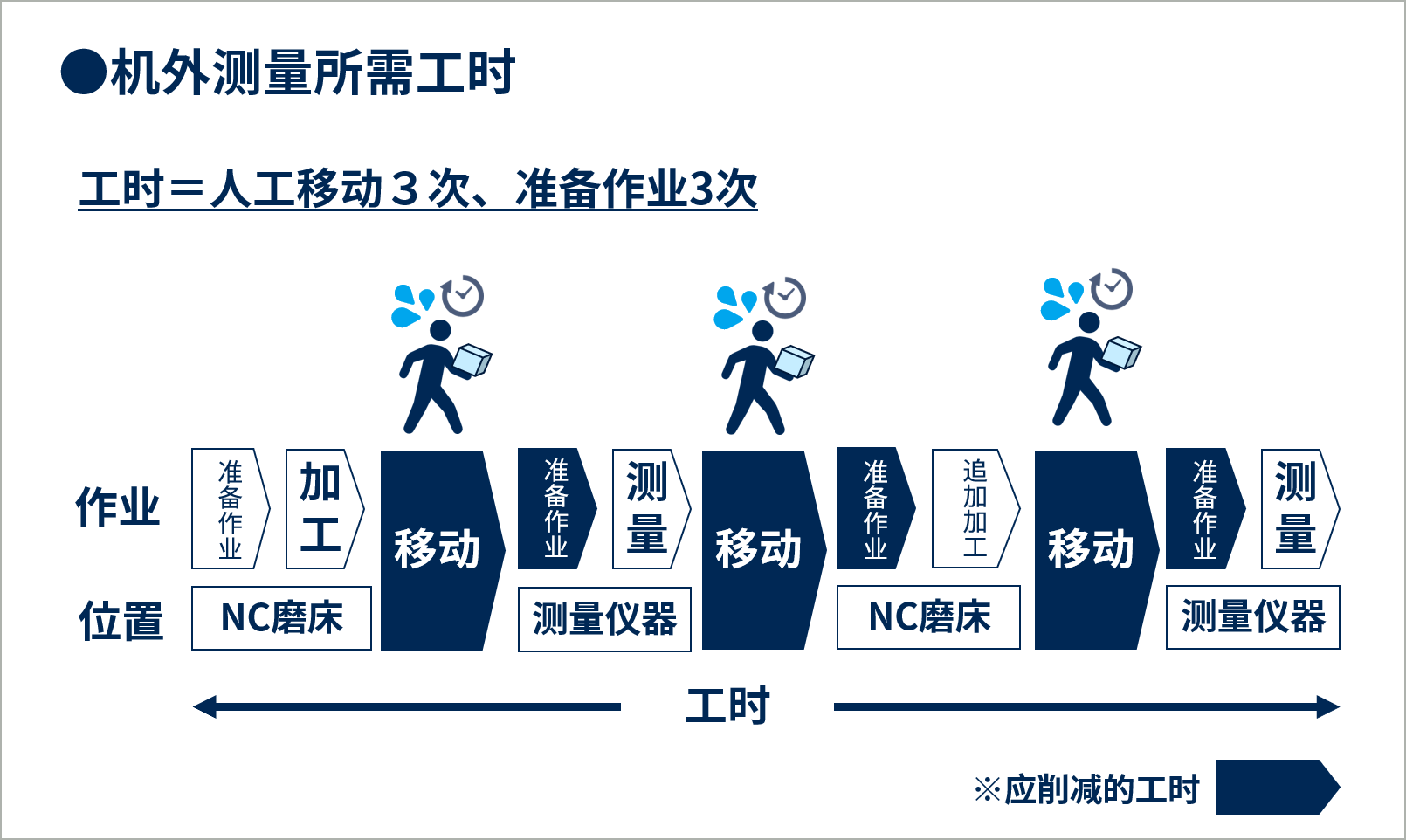
对此,让我们来思考一下机上测量能够改变多少。
通过工时了解“机上测量”的优点
接下来讲解使用接触式探头进行“机上测量”的工时与优点。
从结论来看,机上测量从加工到测量的工序全部在设备上进行,具有以下可削减工时的优点。
- 省去了取出工件的作业
- 省去了再次安装工件的作业
- 无需人员移动
让我们使用与机外测量相同的示例,比较可以削减多少工时。
验证2:模拟机上测量
(例)①加工 ⇒ ② 测量 ⇒ ③ 追加加工⇒ ④测量的周期
与机外测量的模拟比较:
- 人员移动 3次(机外) ⇒ 0次(机内)
- 准备作业 3次(机外) ⇒ 0次(机内)
由此可见,有助于节省工时。(参看下图)
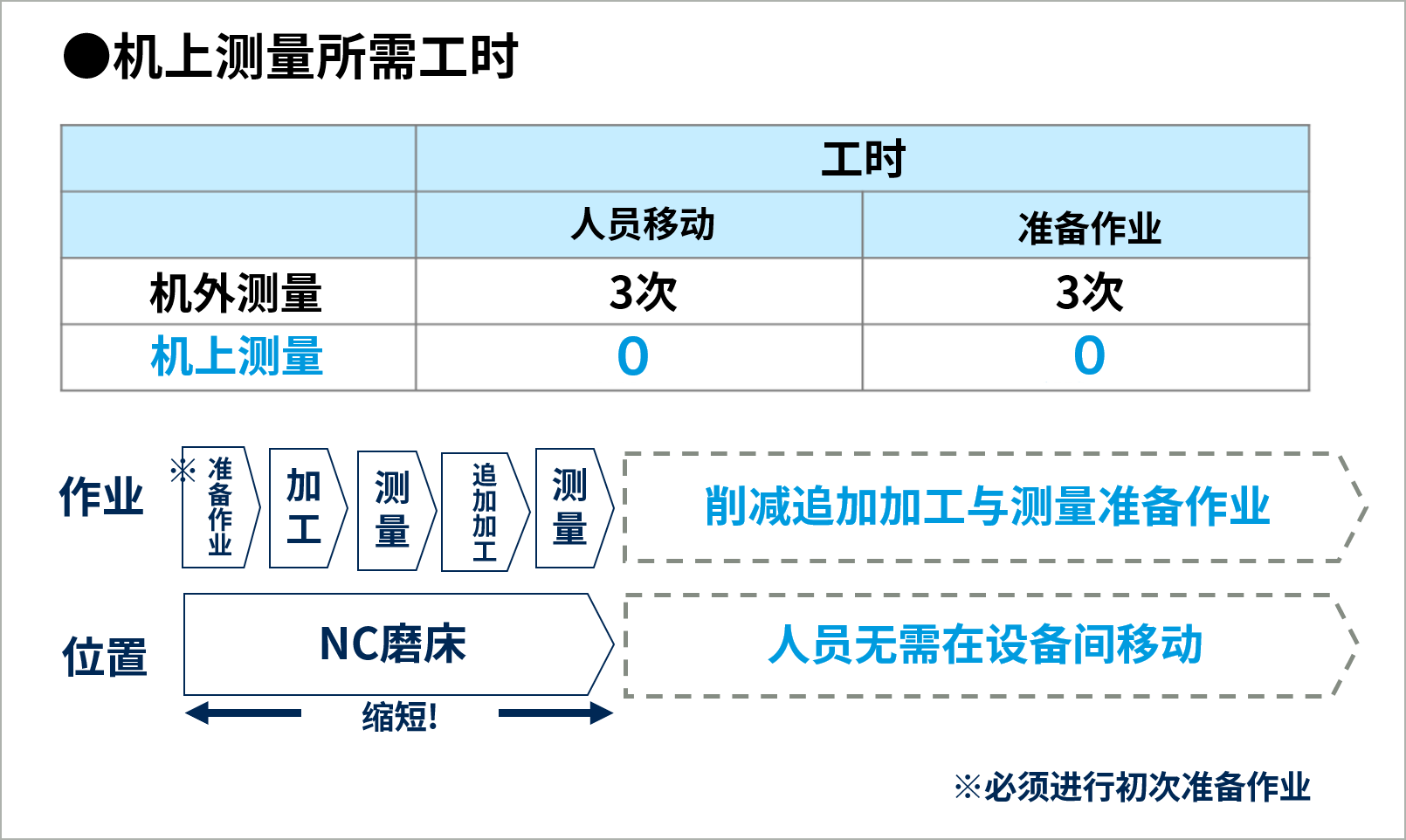
工时比较“机上测量”与“机外测量”
通过比较“机上测量”与“机外测量”,削减的工时差异一目了然。
比如,假设(移动+准备)的1组作业需时20分钟,相比(移动+准备)×3组作业,则可削减将近1小时的时间。
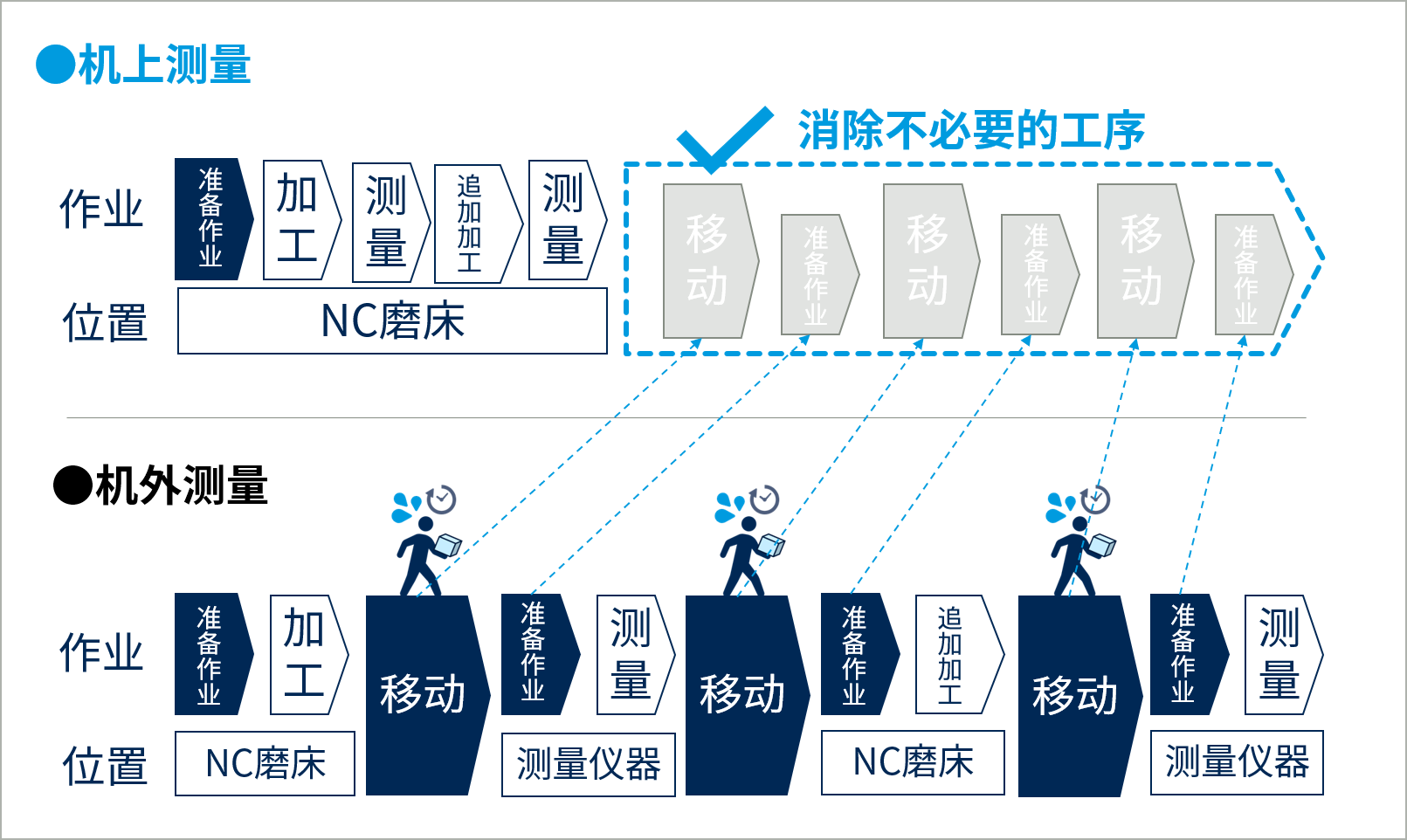
机上测量的测量精度如何?下面是机上测量最适合磨床的理由。
平面磨床适合机上测量的最大理由就是:可以在“对工件进行高精度定位(夹持)的状态下”进行测量这点。
公差要求越严格的工件,重新安装到机械、测量仪器上时所需的时间和手续越多。
若从一开始就无需拆卸工件进行测量,就可在减少麻烦的同时实现高精度测量。
那么,有助于削减工时的机上测量的测量精度可达到何种程度?
比如即使缩短工时,但若测量精度低下,无法达到测量效果亦无济于事。
接下来对机外测量(卡尺)与机上测量的精度进行比较。
验证机上测量的精度(参考数据)
机上测量与机外测量(卡尺)的工件厚度测量数据具体如下。
下图数据表明:机上测量已达到了测量误差低于1μm的高精度水平。
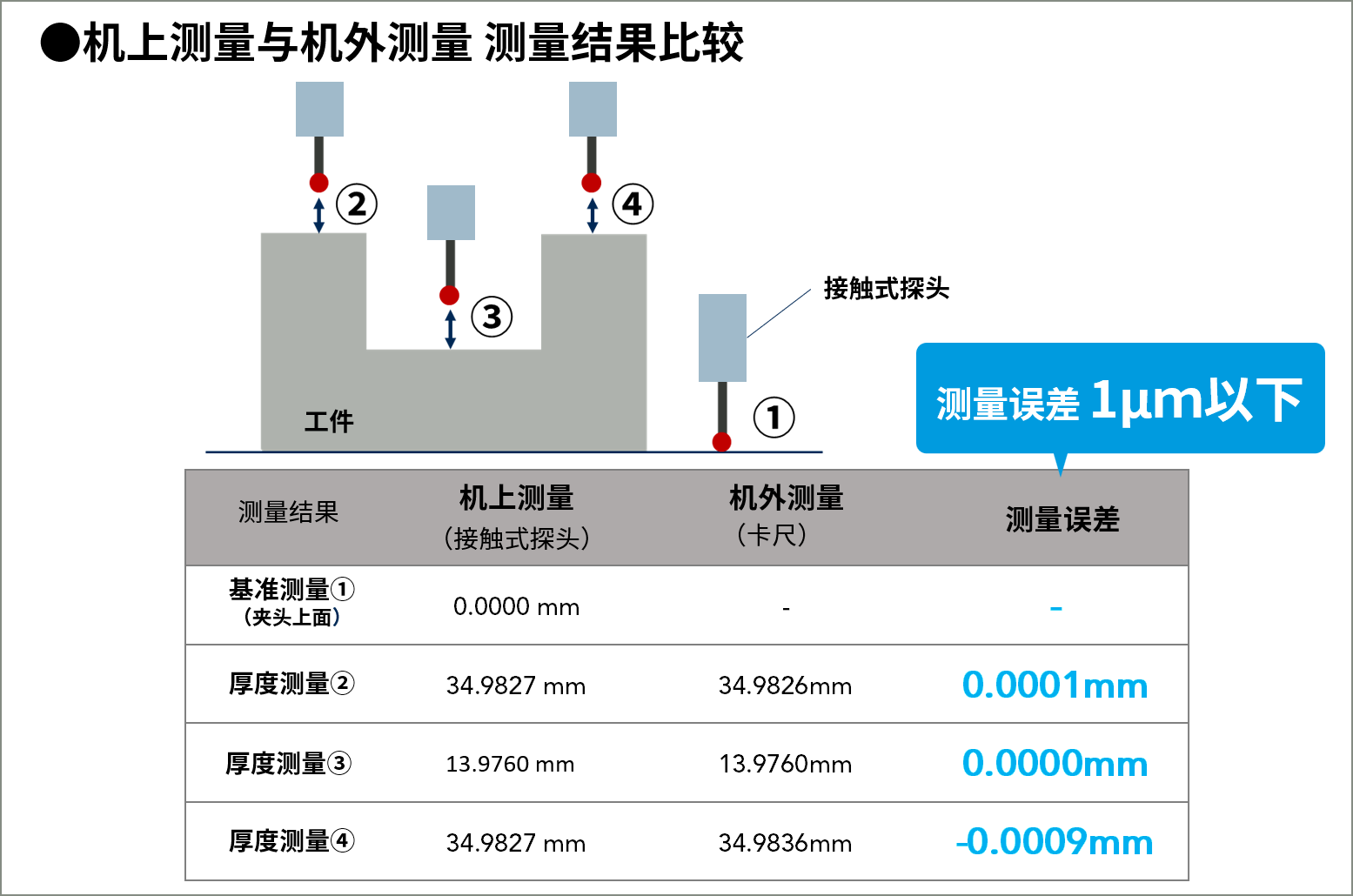
由于机上测量是对加工后的工件进行测量,因此也有部分用户担心根据加工状况及工件材质会出现“因热膨胀引起数微米的尺寸变化”。
但是,重点在于“将测量结果用于削减工时”。
我们可以通过考虑热膨胀系数并在加工现场设置追加加工的标准,探索可削减测量后返工次数等高效使用测量结果的方法。
可进行机上测量的CNC平面磨床的介绍
现在,冈本机床制作所的平面磨床HPG系列可使用机上测量装置“Quick Touch”实施机上测量。
以前对机上测量抱有以下成见:
- 成本高,不可引进
- 无法编程,不可引进
- 担心会损坏探针及传感器
由于此类问题有了得以改善的选项,相比以往便可毫无顾忌地引进机上测量。
- 引进成本低
- 专用软件,无需编程也可使用
- 重复精度1μm的测量精度
【视频】NC磨床机上测量演示
为什么现在机上测量很重要?
① 现在的测量方法是否恰当?市场要求与现场课题的困境。
随着订货方及客户对品质的要求及部件精细化逐年升级,现场所要解决的问题亦不断增加。
- “虽然增加了测量项目,但却无法计入价格,不得不进行无偿检查……”
- “有高价测量仪器,若不使用感觉可惜……”
- “难以确保足够的检查人员”
当然检查需要人手(成本)。
要改善测量规则,首先应重新评估
・当前的测量方法是否过剩?
・是否符合成本要求?
负担大的检查体制可能会发生漏看及错误。
是否可以通过“机上测量”来判定订货方要求的加工品质?应对这一问题进行探讨并做出适当的判断。
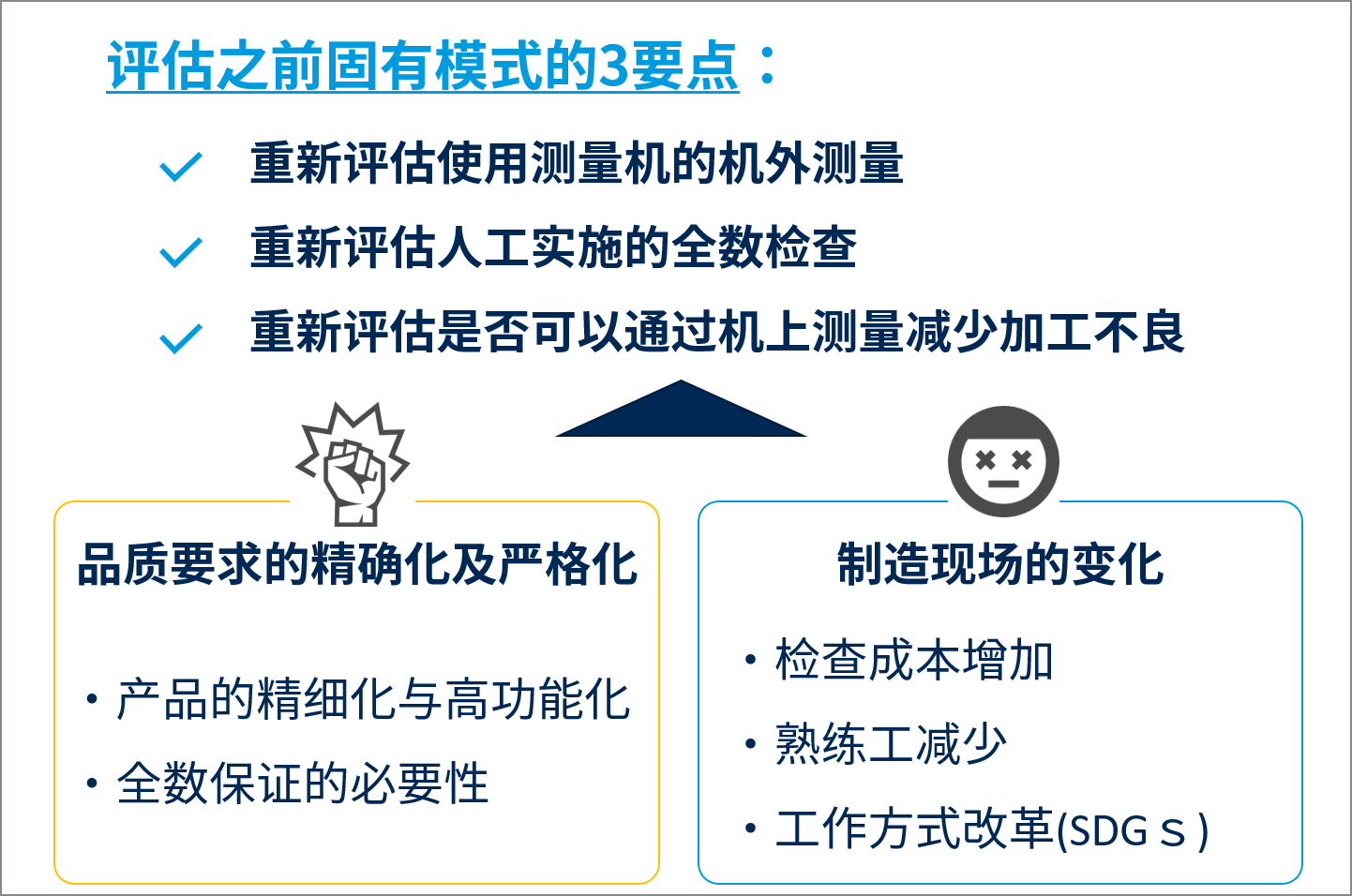
②“因为会降低运转率而不愿进行机上测量!”的观念是否落伍?
由于劳动人口减少,不能“只进行本部门的改善”,还要求“实现跨部门的流程优化”。
一直以来各部门都是优先进行本部门的优化。
・加工部门进行“提高机器运转率”的改善
・检查部门采用人海战术及专用检查线进行杜绝不良的改善
但是,今后更重要的是实现对两部门皆有利的改善。
即使当前没有问题,但如果考虑到5年甚至10年后,当前的组织体制及机制是否还能维持?这些问题不得不引起我们的思考。
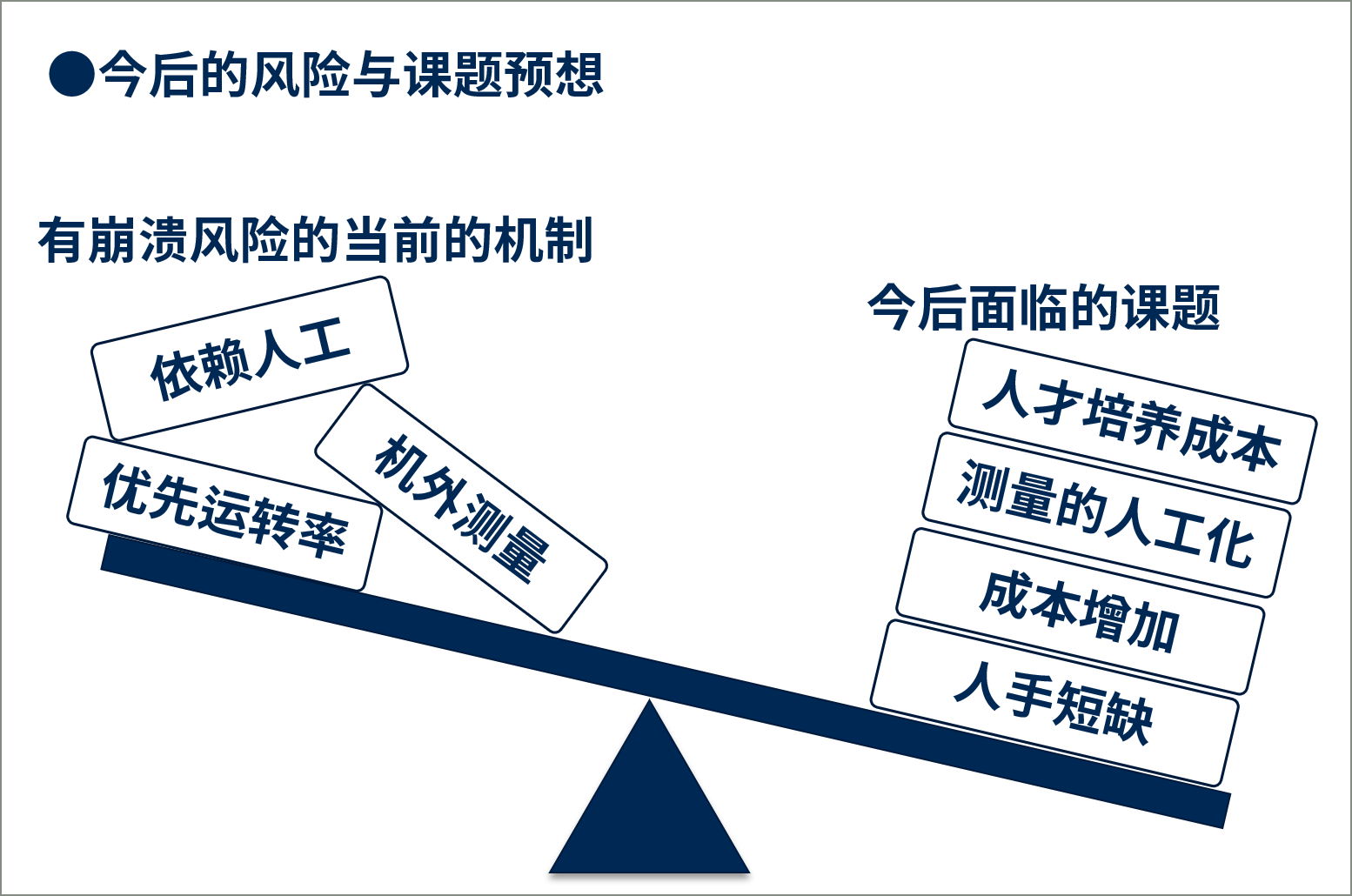
如何区分使用机上测量与三坐标测量机?
测量是确保品质的关键。
加工模具及航空部件等精密部件时,三坐标测量机是可以发挥高可靠性的测量仪器。
亦有大量用户是因订货方的要求而使用三坐标测量机,今后这种仪器在各种场合的需求量将会不断增加。
另一方面,应密切关注
- 温度管理
- 加工部门与测量部门的合作
- 测量仪器操作方法的掌握
- 测量仪自身并不会产生经济价值
等应用和培训所需的总成本。
若是要求精度达到精加工水平的CNC平面研磨,不仅要能进行高精度加工,也必须能实施测量。
若能由机器来完成自动化测量,便有望削减检查作业人员的培训成本,改善人工测量造成的品质不均。
协调组合是最有效的选项。
机上测量的优点与缺点汇总
下面对上述机上测量与机外测量的主要优缺点进行汇总。
<优点>
- 机上测量:削减与人员移动相关的准备作业及工时。
- 机外测量:可以高精度测量。
<缺点>
- 机上测量:与三坐标测量机等比较,测量精度容易受到外界干扰。
- 机外测量:测量所需工时多,测量系统(人、机器、运用)的维护成本高。
其他优缺点汇总如下:
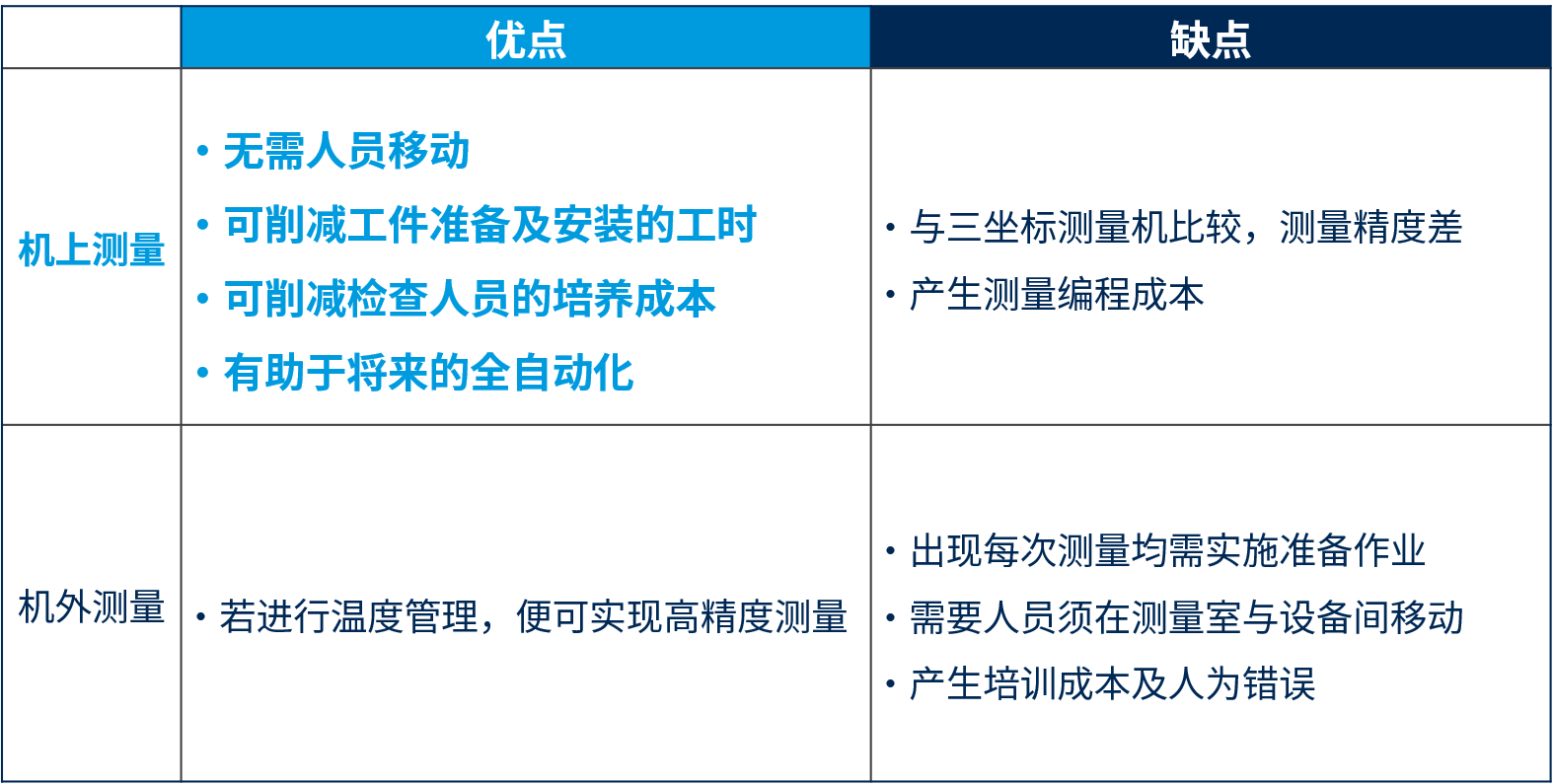
再次强调,测量是验证加工品质的重要工序。
另一方面,测量所需工时的价值也是一个难以被理解的范畴。
在平衡制造与品质管理部门之间需求的同时,作为优化制造现场整体的方法,不妨考虑一下“机上测量”如何?
磨床可使用的机上测量用接触式探头
超小型,省空间,自动定位工件原点
本文将对实现NC平面磨床“砂轮抵磨作业”全自动化的业界先进技术进行讲解。
组合机上测量,实现NC平面磨床准备作业至加工的全自动化的业界首创技术。